Aircraft Accessory Test Bench
HID-300 Series , The Aircraft Accessory Test Bench is a high-performance, multipurpose ground support system designed for the functional testing, troubleshooting, and qualification of various hydraulic, pneumatic, and electro-mechanical components used across civil and military aircraft platforms.
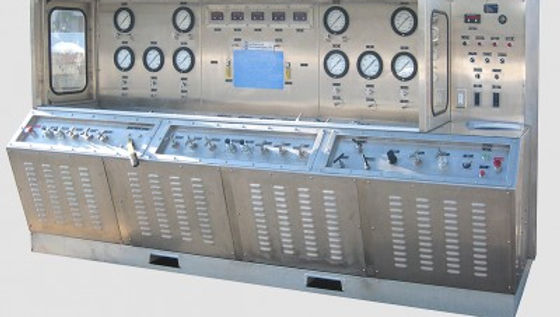
e Aircraft Accessory Test Bench is a high-performance, multipurpose ground support system designed for the functional testing, troubleshooting, and qualification of various hydraulic, pneumatic, and electro-mechanical components used across civil and military aircraft platforms. Developed by Hydraulics International Inc. (HII), this advanced test bench is essential for MRO (Maintenance, Repair, and Overhaul) facilities, OEMs, and aviation research labs that require rigorous and accurate testing procedures under simulated operational conditions.
The system is engineered to accommodate a broad spectrum of aircraft accessories including hydraulic pumps, motors, actuators, valves, accumulators, fuel metering units, pressure regulators, and servo valves. The HID-300 Series is built to support testing up to 5,000 PSI, ensuring it is fully compatible with both older-generation and modern high-pressure aircraft systems.
Equipped with a dual hydraulic supply system (low and high pressure), the unit enables real-time performance verification of accessories across variable load profiles. Its robust high-pressure gear or piston pump can deliver adjustable flow rates—ranging from 0 to 60 GPM—simulating in-service demands. A closed-loop control system maintains accurate pressure regulation, ensuring test consistency and safety.
The test bench includes an integrated instrumentation suite consisting of digital flowmeters, high-accuracy pressure transducers, temperature sensors, and tachometers. All data is displayed on a user-friendly touchscreen HMI (Human Machine Interface) that is connected to an onboard PLC (Programmable Logic Controller). This interface allows users to configure tests, monitor live results, and generate digital test reports.
Filtration is handled through a multi-stage high- and low-pressure filtration system to maintain fluid cleanliness per NAS 1638 Class 6 or better, critical for accurate testing and long component life. The fluid reservoirs, typically ranging from 150 to 300 liters in capacity, are thermally regulated to simulate temperature conditions of in-service aircraft systems.
The unit's versatility is enhanced through modular test panels and connection ports that support quick changes between component types. Safety features include electronic pressure limiting, automatic shut-off, leak detection, and over-temperature alarms. The bench is built on a heavy-duty frame with locking caster wheels, offering both durability and mobility in maintenance hangars or labs.
Applications:
MRO facilities for commercial, military, and business aircraft
OEM production testing and QA/QC validation
Research & development environments for new hydraulic component design
Certification and verification testing in compliance with aerospace standards
Functional fault isolation and performance validation during overhaul cycles
Technical Specifications Table:
Specification | Details |
Part Number | HID-300 Series |
Test Pressure Range | 0 – 5,000 PSI |
Flow Rate | Up to 60 GPM |
Supported Components | Pumps, valves, actuators, regulators, servo valves, accumulators |
Hydraulic Fluids | MIL-H-5606, MIL-PRF-83282, Skydrol, HyJet |
Filtration | Multi-stage; NAS 1638 Class 6 or better |
Instrumentation | Pressure transducers, digital flowmeters, temp sensors, tachometers |
Control Interface | PLC-controlled HMI touchscreen |
Reservoir Capacity | 150 – 300 liters with heating/cooling |
Power Supply | Electric (3-phase, typically 380–480V, 50/60Hz) |
Mobility | Heavy-duty frame with caster wheels |
Safety Features | Overpressure shutoff, temp alarms, leak detection |
Applications | MRO, R&D, OEM, quality assurance |
Get in Touch
AVA AERO Trading LLC
Dubai, UAE