Pump system design is a critical process that involves selecting and configuring the right equipment and piping components to achieve optimal performance. Inadequate design can lead to poor system efficiency, excessive energy consumption, and reduced reliability. Therefore, it is important to consider various factors during the design phase to ensure that the pump system functions effectively and efficiently.

Keywords: pump system design, piping design, system curves, pump curves, friction losses, flow control, pressure control, pump types, efficiency, reliability
System Requirements: The first step in pump system design is to determine the system requirements, such as flow rate, head pressure, and fluid properties. The system requirements determine the pump type and size, which will deliver the desired performance. Additionally, the designer must consider the available space, power supply, and budget.
Pump Type: The pump type must match the system requirements, fluid characteristics, and application. Centrifugal pumps are commonly used in many applications due to their high flow rates and low head pressure. Positive displacement pumps are ideal for low flow and high-pressure applications, while axial flow and mixed flow pumps are ideal for high flow and low head applications.
Pump Selection: Once the pump type is determined, the designer must select the appropriate pump model and size that will deliver the desired flow rate and head pressure. Pump curves and system curves are used to determine the optimal pump selection.
Piping Design: Proper piping design is crucial to ensuring that the pump operates efficiently and effectively. The designer must consider the friction losses, which are caused by the flow of fluid through the pipe. The diameter, length, and material of the pipe impact the friction losses, which can increase energy consumption and reduce pump performance.
Flow Control: Controlling the flow rate is critical to maintaining pump efficiency and preventing cavitation. Flow control valves, such as throttling valves, pressure control valves, and bypass valves, can be used to regulate the flow rate.
Pressure Control: The system pressure must be controlled to prevent overloading the pump and damaging the system components. Pressure relief valves and pressure regulators are used to maintain the system pressure within the desired range.
Pump Efficiency: The pump's efficiency impacts the overall system efficiency and operating costs. Therefore, the designer must select a pump with a high efficiency rating and design the system to operate at the optimal flow rate and head pressure.
Reliability: Pump reliability is critical in preventing system failures and reducing maintenance costs. The designer must select a pump with a proven track record of reliability and design the system to prevent potential issues, such as cavitation, air entrainment, and sediment accumulation.
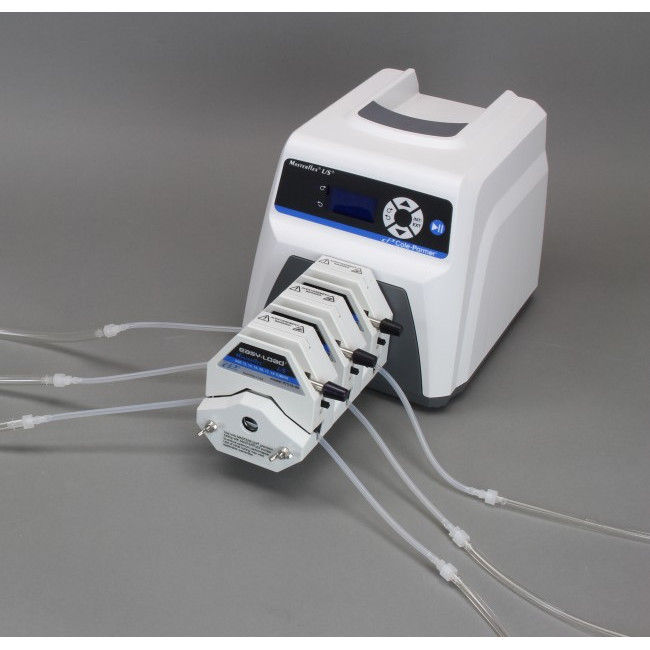
In conclusion, pump system design is a complex process that requires careful consideration of various factors. The designer must select the appropriate pump type and size, design the piping system to minimize friction losses, control the flow rate and pressure, ensure optimal pump efficiency, and prioritize system reliability. By following these considerations, pump systems can achieve optimal performance, reduce energy consumption, and lower operating costs.
Comments