One and Done: Understanding Single Stage Centrifugal Pumps
- ADMIN
- Mar 27, 2023
- 3 min read
Introduction:
Single stage centrifugal pumps are a type of centrifugal pump that have one impeller and are commonly used for low-pressure applications. These pumps are known for their simple design and cost-effectiveness. In this article, we will provide a comprehensive guide to single stage centrifugal pumps, including their design, operation, and applications.
Design:
Single stage centrifugal pumps have a relatively simple design compared to multi-stage pumps. They consist of an impeller, casing, shaft, bearings, and mechanical seals. The impeller is the key component that generates the centrifugal force required to transfer the fluid. The casing surrounds the impeller and directs the flow of fluid through the pump. The shaft connects the impeller to the motor, and the bearings support the shaft. Finally, mechanical seals prevent leakage of fluid from the pump.
Operation:
When the impeller of a single stage centrifugal pump rotates, it creates a flow of fluid through the pump. The fluid enters the pump through the inlet and is directed towards the center of the impeller. As the fluid flows through the impeller, the impeller's vanes impart energy to the fluid, causing it to move radially outward. This centrifugal force pushes the fluid out of the impeller and into the casing, where it is directed towards the outlet.
Applications:
Single stage centrifugal pumps are commonly used in a variety of low-pressure applications, including water transfer, irrigation, drainage, and air conditioning systems. These pumps are also used in applications where the fluid being transferred is relatively clean and free of solids. Single stage pumps are not suitable for high-pressure applications or applications where the fluid being transferred contains a high concentration of solids.
Selection Criteria:
Selecting the right single stage centrifugal pump for your application requires consideration of several factors, including flow rate, head pressure, NPSH requirements, and efficiency.
Flow R

ate:
The flow rate of a single stage centrifugal pump is determined by the diameter of the impeller and the speed of rotation. Increasing the impeller diameter or the speed of rotation will increase the flow rate. It is important to select a pump with a flow rate that matches the required flow rate of the system.
Head Pressure:
The head pressure of a single stage centrifugal pump is determined by the impeller diameter, the speed of rotation, and the design of the pump casing. Increasing the impeller diameter or the speed of rotation will increase the head pressure. It is important to select a pump with a head pressure that matches the required pressure of the system.
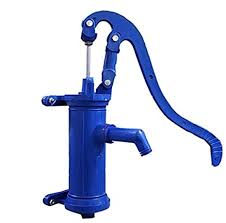
NPSH:
NPSH requirements refer to the minimum amount of pressure required at the inlet of the pump to avoid cavitation. Cavitation occurs when the pressure at the inlet of the pump drops below the vapor pressure of the fluid, causing bubbles to form. These bubbles can collapse and cause damage to the impeller and other pump components. It is important to select a pump with NPSH requirements that match the available inlet pressure of the system.
Efficiency:
Efficiency refers to the energy required to operate the pump and the maintenance costs associated with the pump. Selecting a pump with high efficiency can result in significant energy savings over the lifetime of the pump. It is also important to consider the maintenance requirements of the pump and the availability of replacement parts.
Advantages:
Single stage centrifugal pumps have several advantages over other types of pumps. They are simple in design and have a low initial cost. They are also easy to install and operate, and require minimal maintenance. Single stage pumps are suitable for applications where the fluid being transferred is relatively clean and free of solids, making them a popular choice for water transfer and irrigation systems.
Disadvantages:
While single stage centrifugal pumps are effective for low-pressure applications, they are not suitable for high-pressure applications or applications where the fluid being transferred contains a high concentration of solids. They also have lower efficiencies compared to multi-stage pumps, meaning they consume more energy for the same flow rate.
Conclusion:
Single stage centrifugal pumps are a cost-effective and efficient choice for low-pressure applications where the fluid being transferred is relatively clean and free of solids. Their simple design and ease of installation make them a popular choice for water transfer, irrigation, and air conditioning systems. When selecting a single stage centrifugal pump, it is important to consider factors such as flow rate, head pressure, NPSH requirements, and efficiency. By considering these factors, you can ensure that your single stage centrifugal pump operates efficiently and effectively for your specific application.
Comments