The F-15 GSE: Powering a Legacy of Excellence Through Advanced Ground Support
- ADMIN
- Jan 20
- 11 min read
Introduction of F-15 Eagle

Few fighter jets in history can match the storied legacy of the F-15 Eagle. Conceived during the Cold War as a response to emerging aerial threats, this aircraft quickly proved its worth with unmatched speed, agility, and firepower. Designed by McDonnell Douglas (now part of Boeing) and introduced in 1976, the F-15 has undergone numerous technological updates to maintain its status as a formidable air superiority fighter. Yet, the true key to its enduring success lies not just in flight performance but also in an often-overlooked asset on the ground: F-15 GSE (Ground Support Equipment).
Ground Support Equipment comprises the tools, machinery, and systems that maintain and prepare the F-15 before and after each flight. In this in-depth blog post, we will explore how F-15 GSE supports the fighter’s exceptional performance, delve into various types of specialized equipment—both common and more advanced—and discuss why high-quality, American-made GSE is vital. Whether you are an aviation professional, an aspiring pilot, or a dedicated enthusiast, understanding the significance of F-15 GSE will deepen your appreciation for how each mission is made possible.
1. A Brief History of the F-15
1.1 Development and Design Philosophy

The F-15 project began in the late 1960s to counter next-generation Soviet fighters. Its design emphasized air superiority, focusing on raw speed, climb rate, maneuverability, and firepower. The resulting aircraft leveraged advanced avionics, lightweight materials, and powerful turbofan engines to achieve an impressive thrust-to-weight ratio. Initial flight tests in 1972 quickly demonstrated these capabilities, and by 1976, the F-15 had entered active service with the U.S. Air Force.
1.2 Evolving Capabilities
Over the years, the F-15 Eagle has undergone iterative enhancements. Variants such as the F-15C improved air-to-air combat performance, while the F-15E Strike Eagle introduced robust ground-attack capabilities. Upgrades have included AESA (Active Electronically Scanned Array) radars, data links, and improved cockpit interfaces. Despite newer aircraft entering service, the F-15 remains a cornerstone of multiple air forces worldwide, underscoring the success of its fundamental design.
1.3 The Importance of GSE for the F-15
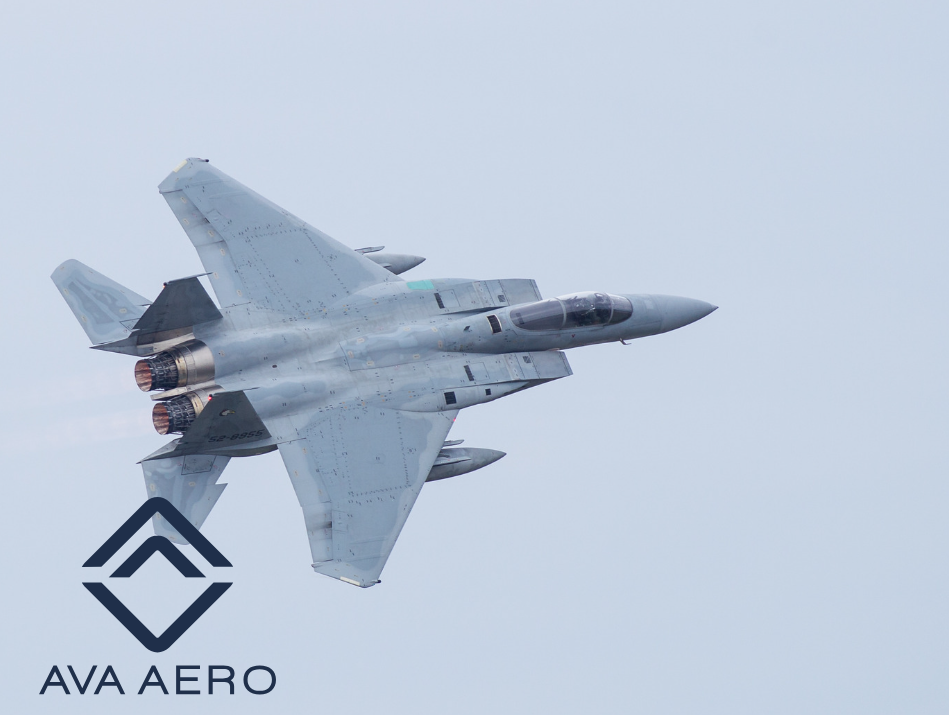
Regardless of how capable the aircraft is in the sky, it demands meticulous care on the ground. This is where F-15 GSE comes into play, ensuring every component—electronics, hydraulics, engines, and more—works flawlessly. High-quality GSE reduces turnaround time, prevents failures, and extends the overall service life of the fleet.
2. Defining F-15 GSE
Ground Support Equipment (GSE) encompasses all the specialized equipment needed to service, inspect, and maintain an F-15 while it is not in flight. From diagnostic devices that pinpoint system faults to hydraulic power units that keep control surfaces operational, GSE covers a broad spectrum. Because the F-15’s technology is complex and ever-evolving, GSE must be equally sophisticated, durable, and precise.
2.1 Core Functions of F-15 GSE
Pre-Flight Preparation- Checks for avionics, power systems, hydraulic and pneumatic components.- Supplies air-conditioning and electrical power for cockpit instruments.
Post-Flight Maintenance- Inspections for wear, mechanical integrity, and potential damage.- Refueling, hydraulic fluid replenishment, and system data recording.
Scheduled Overhauls and Repairs- Deep-level checks on engines, avionics, and structural elements.- Replacement of parts and thorough cleaning to prevent corrosion.
Emergency and Battle-Damage Repairs- Rapid diagnostics and part swaps under high-pressure scenarios.- Specialized kits designed to address common or mission-specific damage.
GSE thus forms an invisible yet indispensable backbone that ensures the F-15 can safely and efficiently return to the skies time and again.
3. Why American-Made F-15 GSE Matters
While GSE can be produced worldwide, American-made F-15 GSE has unique advantages:

Compliance with Stringent Quality Standards American manufacturers adhere to strict regulations and testing protocols. These high standards minimize the risk of premature failures or performance issues.
Comprehensive Documentation and Support U.S. manufacturers often provide detailed technical manuals, robust customer service, and spare parts availability, facilitating seamless maintenance and troubleshooting.
Seamless Integration Given that the F-15 was designed in the United States, American-made GSE typically aligns best with the aircraft’s technical requirements, from power specifications to software compatibility.
Regulatory Ease FAA and U.S. military standards are recognized globally, making it simpler to ensure compliance across different international jurisdictions.
For nations or organizations operating the F-15, these factors can significantly streamline maintenance processes and reduce long-term operating costs.
4. Key Considerations When Selecting F-15 GSE
4.1 Compatibility with Advanced Systems
The F-15’s avionics, fly-by-wire controls, and sensors require ground equipment that matches precise specifications. Even small mismatches in voltage, frequency, or calibration can cause inaccurate diagnostic readings, leading to larger issues if undetected.

4.2 Reliability Under Stressful Conditions
F-15 squadrons deploy worldwide—into deserts, jungles, and polar climates. GSE must withstand extreme temperatures, high humidity, or dusty environments. A fragile piece of equipment could fail at a critical moment, jeopardizing both missions and safety.
4.3 Maintainability and Ease of Use
User-friendly designs not only help ground crews work more efficiently but also reduce training times. Furthermore, GSE with accessible parts and straightforward repair procedures lowers overall maintenance costs and downtime.
4.4 Safety Features
Proper safety measures—such as lockout/tagout systems, emergency shutoffs, and protective barriers—are essential. Handling powerful machinery or dealing with high-pressure fluids can be hazardous if not managed with care.
4.5 Compliance and Certification

Meeting official certifications (e.g., military standards, ISO quality management) confirms that GSE has passed rigorous testing. Operating uncertified equipment can lead to regulatory penalties, insurance issues, or critical failures.
5. Common and Advanced F-15 GSE: An Overview
Below is a wide-ranging look at the GSE categories crucial for keeping the F-15 at peak performance. While some of these are standard across many military aircraft, others are specific to the unique demands of the F-15.
5.1 Hydraulic Power Unit (HPU)

Purpose: Supplies pressurized hydraulic fluid to power the F-15’s control surfaces, landing gear, brakes, and other critical subsystems during ground maintenance.
Key Features:
- High-Pressure Capability: Must deliver pressure consistent with F-15 requirements (up to 3,000 psi or more).
- Filtration: Removes contaminants to protect sensitive valves and actuators.
- Fluid Reservoir Management: Monitors fluid levels and temperature to prevent aeration or overheating.
A reliable HPU is indispensable for routine checks and any deeper-level servicing of the aircraft’s hydraulic system.
5.2 Hydraulic Test Units
Purpose: Perform diagnostic evaluations, leak checks, and dynamic tests on the aircraft’s hydraulic circuitry.
Technical Considerations:
- Precision Gauges: Must accurately measure psi to detect even minor system leaks.
- Automation: Some modern units integrate computer controls for streamlined, repeatable testing.
- Data Logging: Creates a record of tests for traceability and troubleshooting.
Though similar to HPUs, Hydraulic Test Units are more focused on monitoring performance and detecting issues rather than simply supplying power.

5.3 Cabin Leakage Tester
Purpose: Evaluates the integrity of the F-15’s cockpit and pressurization system, ensuring minimal leakage.
Key Features:
- Regulated Pressure: Simulates flight conditions to check how well cabin seals hold air.
- Digital Monitoring: Modern testers may track pressure gradients over time for precise data.
- Portability: Designed to be moved around the aircraft easily, offering quick setups.
A pressurized cockpit is vital for pilot safety and comfort, making a cabin leakage tester an essential piece of F-15 GSE.
5.4 Instrument Verification System
Purpose: Calibrates and verifies the accuracy of the F-15’s flight instruments (e.g., altimeters, airspeed indicators, angle of attack sensors).
Technical Considerations:
- High-Fidelity Sensors: Must reproduce flight-like conditions accurately.
- Software Integration: Communicates with onboard avionics to confirm consistent data exchange.
- Multi-Instrument Compatibility: Can verify various instruments in a single session.
Accurate readings are non-negotiable in high-performance jets like the F-15, making instrument verification systems a cornerstone of safe operations.
5.5 Ground Power Units (GPU)
Purpose: Provide external electrical power to the F-15 during ground operations, supporting avionics and tests without running the jet’s engines.
Key Features:
- Voltage/Phase Control: Must match the F-15’s specific power requirements (commonly 115 VAC, 400 Hz, three-phase).
- Load Capacity: Adequate amperage to power multiple onboard systems.
- Environmental Robustness: Withstands temperature extremes and other environmental stressors.
GPUs play a crucial role in pre-flight and post-flight checks, powering up instrumentation, radar systems, and communication devices.

5.6 Air Conditioning Carts
Purpose: Provide temperature-controlled air to the cockpit and avionics compartments, preventing overheating or damage to sensitive electronics on the ground.
Technical Considerations:
- Variable Output: Adapts airflow and temperature based on ambient conditions.
- Filtration: Removes particulates that could harm avionics.
- Noise Reduction: Minimizes acoustic interference for ground crew.
Proper climate control ensures pilot comfort and electronics reliability, both critical for mission success.
5.7 Nitrogen/Oxygen Carts
Purpose: Store and supply gases necessary for pneumatic systems (tires, ejection seat mechanisms, etc.) and life support (pilot oxygen systems).
Key Features:
- High-Pressure Tanks: With regulators tuned to safe operating levels.
- Gas Purity Sensors: Oxygen must meet medical-grade standards.
- Multi-Port Output: Supports simultaneous servicing of multiple systems.
These carts address fundamental safety needs, providing the lifeblood of pneumatic and life support systems.
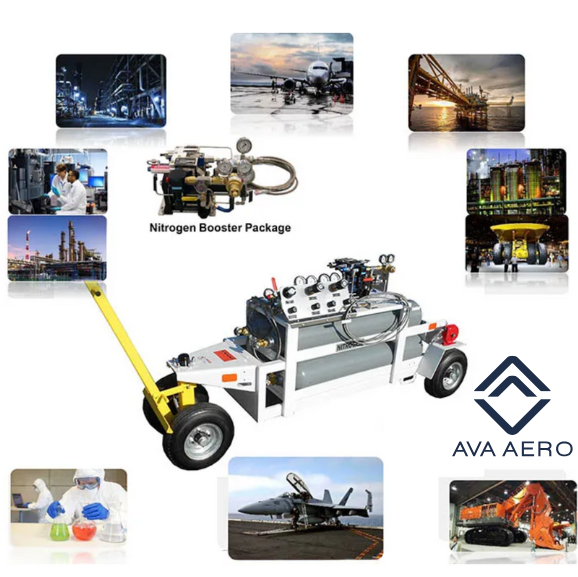
5.8 Maintenance Platforms
Purpose: Offer secure, stable access for technicians performing maintenance on the airframe, wings, and tail sections.
Technical Considerations:
- Adjustable Height: Ensures ergonomically safe working positions.
- Safety Rails and Non-Slip Surfaces: Reduces risk of falls.
- High Weight Capacity: Accommodates both personnel and tools.
Effective maintenance platforms help crews work quickly and safely, lowering the risk of accidental damage to the aircraft.
5.9 Engine Stands
Purpose: Facilitate removal, transportation, and reinstallation of the F-15’s turbofan engines.
Key Features:
- Robust Construction: Must handle the engine’s weight and secure it firmly.
- Mobility: Usually equipped with casters for maneuverability.
- Adaptable Mounts: Compatible with different F-15 engine variants (e.g., Pratt & Whitney F100 or other upgraded models).
Quality engine stands make the daunting task of engine overhauls much more efficient and safer.
5.10 Towbars
Purpose: Attach to the F-15’s landing gear for ground towing.
Technical Considerations:
- Precision Fit: Matches the aircraft’s nose or main landing gear dimensions.
- Materials: Often aluminum or steel for a strong yet lightweight frame.
- Compatibility with Tugs: Ensures stable maneuvering around the airbase.
Safe towing prevents wear and tear on landing gear and reduces the risk of collisions.
5.11 Corrosion Control Cart
Purpose: Supports cleaning, surface treatment, and corrosion prevention operations on F-15 airframes and components.
Key Features:
- Chemical Handling: Includes tanks or sprayers for anti-corrosion solutions.
- Waste Collection: Manages runoff or spent chemicals to protect the environment.
- Safety Systems: Protective gear and ventilation to safeguard technicians.
Given the diverse climates and operational environments the F-15 encounters, preventing corrosion extends the aircraft’s life and reliability.
5.12 Fluid Servicing Units
Purpose: Handle the transfer and filtration of various critical fluids (coolants, specialized cleaning solutions, etc.) required for F-15 subsystems.
Technical Considerations:
- Proper Seals: Avoid leaks that could compromise fluid purity.
- Compatible Couplings: Must match the F-15’s fluid connectors.
- Monitoring and Measurement: Gauges to confirm correct fluid volume and flow rates.
Fluids beyond fuel and hydraulic fluid—such as coolants or de-icing solutions—are crucial for maintaining the aircraft’s operational readiness.
5.13 Oil Servicing Units
Purpose: Ensure correct engine and gearbox lubrication, vital for the F-15’s high-performance powerplants.
Key Features:
- Temperature Control: Keeps oil at the proper viscosity during servicing.
- Precise Metering: Delivers exact quantities, avoiding both under- and over-servicing.
- Filtration: Removes contaminants that could harm engine components.
Regular oil servicing extends engine life and maintains optimal power output.
5.14 Transmission Fluid Servicing Units
Purpose: Service and maintain the various transmissions or gearboxes within the F-15’s powertrain, ensuring smooth power transfer from the engines to subsystems.
Technical Considerations:
- Fluid Compatibility: Specific additives and friction modifiers suitable for F-15 gearboxes.
- Pressure Control: Avoids surges that could damage delicate seals.
- Easy Draining and Recycling: Facilitates eco-friendly disposal of old fluids.
Transmission fluid is often overlooked, but proper servicing is critical for reliable flight control and accessory drive operation.
6. Technical Deep Dive: Avionics, Diagnostics, and F-15 GSE
The F-15’s cutting-edge avionics—ranging from radar systems to flight control computers—require highly specialized diagnostics. Instrument Verification Systems and Hydraulic Test Units, for instance, gather sensor data in real time, identifying any anomalies in control surfaces or cockpit instruments. Likewise, a stable source of electrical power from GPUs ensures that onboard diagnostics can run accurately without fluctuation.
By aligning precisely with the F-15’s avionics architecture, these GSE elements help technicians detect, record, and address potential faults before they escalate into in-flight emergencies. This proactive approach to maintenance enhances both safety and operational effectiveness.
7. Operational Benefits of High-Quality F-15 GSE
Reduced Downtime- Proper GSE allows for rapid troubleshooting and repairs, ensuring shorter turnaround times between flights.
Extended Service Life- By accurately monitoring systems and regularly replacing worn components, operators avoid costly, large-scale overhauls.
Enhanced Safety- Less risk of mechanical failures mid-flight, thereby protecting both pilots and mission objectives.
Cost Savings- Preventive maintenance performed using reliable GSE is more cost-effective than corrective actions after a system breakdown.
Consistent Performance- The F-15’s well-documented track record of reliability is heavily reliant on top-tier ground support.
8. Best Practices for Managing and Maintaining F-15 GSE
8.1 Scheduled Inspections and Calibration
Regular Servicing: Adhere to strict service intervals for each piece of GSE—particularly those handling high-pressure fluids or sensitive electronics.
Calibration Checks: Ensure measurement instruments (pressure gauges, flow meters, load sensors) remain within specified tolerances.
8.2 Comprehensive Training
Operator Certification: Ground crews should receive hands-on training, along with periodic refreshers to stay updated with new systems.
Safety Protocols: Emphasize lockout/tagout procedures, emergency stops, and proper handling of chemicals.
8.3 Inventory Management
Asset Tracking: Use barcodes or RFID to keep tabs on each piece of GSE, ensuring it’s available when needed.
Spare Parts: Maintain a ready supply of critical spares to avoid prolonged equipment downtime.
8.4 Updates and Modernization
Software Upgrades: For diagnostic systems and test units, firmware or software updates can enhance functionality or fix bugs.
Component Upgrades: Replace aging pumps, motors, or hoses with newer, more efficient technologies.
8.5 Safety Audits
Regular Assessments: Inspect for worn cables, loose fittings, hose, or other potential hazards.
Documentation: Keep detailed records of each audit, including corrective actions taken.
9. The Future of F-15 GSE
As aviation technology continues to advance, so too does GSE:
Smart Sensors and IoT Integration- Ground equipment may soon relay real-time data to a central monitoring system, predicting failures before they occur.
Eco-Friendly Solutions- Electric GPUs, cleaner hydraulic fluids, and reduced emissions are increasingly in demand for environmental sustainability.
Augmented Reality (AR) Maintenance- Techs could wear AR headsets overlaying schematics or step-by-step guides, boosting efficiency and accuracy.
AI-Driven Diagnostics- Machine learning algorithms might analyze sensor data, offering predictive maintenance schedules tailored to each aircraft’s usage profile.
Embracing these innovations will ensure the F-15’s ground support keeps pace with its cutting-edge developments in the air.
Conclusion
The F-15 Eagle is undoubtedly a marvel of modern aerospace engineering—renowned for its speed, agility, and combat track record. However, behind every successful sortie is an intricate support network that ensures the aircraft’s readiness on the ground. F-15 GSE—from Hydraulic Power Units and Cabin Leakage Testers to Corrosion Control Carts and Transmission Fluid Servicing Units—provides the essential foundation for this jet’s continued excellence.
Investing in high-quality, American-made GSE ensures compatibility with the F-15’s advanced systems, delivering the reliability, safety, and efficiency demanded by top-tier military aviation. By adhering to best practices—such as regular calibration, stringent safety protocols, and ongoing modernization—operators can minimize downtime, extend aircraft lifespan, and maintain the F-15’s hard-earned reputation for performance.
Staying well-informed on the latest GSE technologies is not just a matter of operational necessity; it is also crucial for anyone passionate about aviation. When ground crews and decision-makers fully understand the roles and capabilities of GSE, they can make more informed choices that keep the F-15 at the apex of fighter design. Ultimately, the legacy of this iconic aircraft depends on both the engineering brilliance that takes flight and the equally impressive support that remains on the ground.
Educating yourself about F-15 GSE—its functions, advancements, and best practices—ensures this legendary aircraft continues to soar while maintaining a robust foundation of safety, efficiency, and innovation.
Comments