The Importance of Maintenance and Serviceability in Pump Performance
- ADMIN
- Apr 12, 2023
- 2 min read
Pumps are critical components in various industries, from water treatment and distribution to chemical processing and oil and gas production. They transfer fluids from one point to another, and their performance can significantly impact the overall operation of a system. Therefore, it is crucial to ensure that pumps operate efficiently and reliably, and that any issues are promptly identified and resolved. This is where maintenance and serviceability come into play.
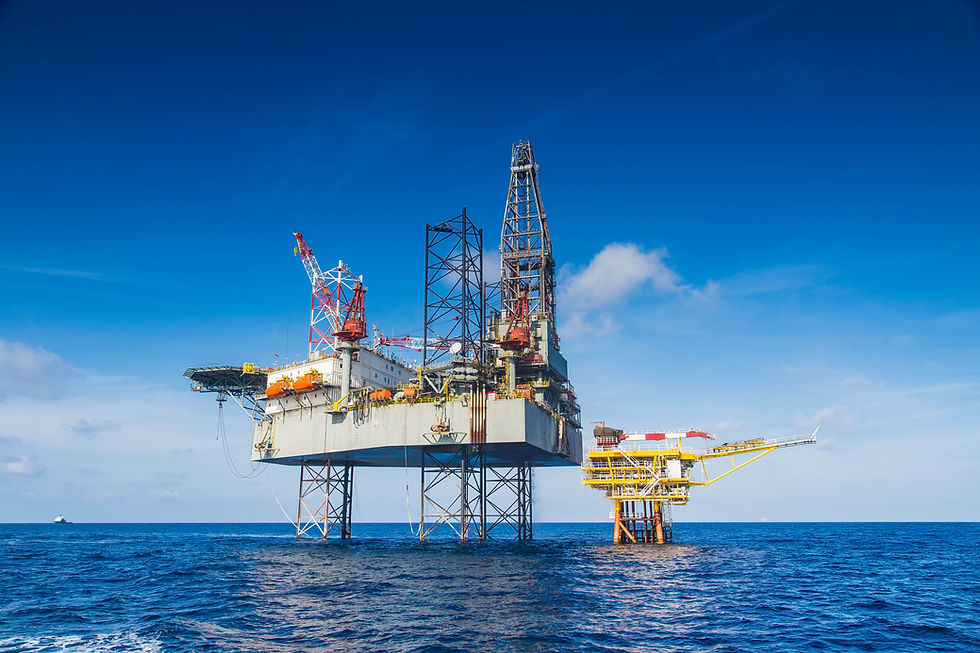
Maintenance is essential to ensure that pumps operate at their optimal performance and reliability levels. There are two primary types of maintenance: preventive and predictive. Preventive maintenance involves routine inspections, cleaning, and replacement of parts to prevent failures and downtime.
Predictive maintenance, on the other hand, uses data and analytics to identify potential issues before they occur. It involves monitoring pump performance, collecting and analyzing data, and identifying trends and patterns to predict future failures. By implementing a comprehensive maintenance program that combines both preventive and predictive maintenance, pump downtime can be minimized, and reliability can be improved.
Serviceability is another critical aspect of pump performance. It refers to how easy it is to access and repair or replace pump components. In many cases, pumps are installed in hard-to-reach locations, such as underground or in confined spaces, making access for maintenance and repair difficult. Therefore, designing pumps with serviceability in mind can save time and money when maintenance or repair is required. For example, pumps with easy-to-remove components or with modular designs can be serviced or replaced quickly, reducing downtime and minimizing the impact on operations.

Condition monitoring is a valuable tool for maintaining and servicing pumps. It involves collecting data on various pump parameters, such as flow rate, pressure, temperature, and vibration, and analyzing it to identify potential issues. By continuously monitoring pump performance, deviations from normal operating conditions can be detected, and corrective actions can be taken before failures occur. Condition monitoring can also be used to optimize pump performance and energy efficiency.
When maintenance or repair is required, it is essential to have a reliable and efficient repair process in place. This includes having access to replacement parts, qualified personnel, and proper tools and equipment. Pumps should be designed with the ease of repair in mind, with clear instructions and diagrams available to aid in the repair process.
Finally, pump replacement should also be considered as part of a maintenance plan. Over time, pumps can become outdated or no longer suitable for their intended application. In such cases, replacing the pump may be the best option to ensure optimal performance and reliability. Pump replacement can also result in energy savings and reduced operating costs, as newer pumps are often more efficient than older models.

In conclusion, maintenance and serviceability are critical to pump performance, reliability, and uptime. Implementing a comprehensive maintenance program that includes both preventive and predictive maintenance, monitoring pump performance through condition monitoring, and designing pumps with serviceability in mind can reduce downtime and minimize the impact on operations. Having a reliable and efficient repair and replacement process in place can also ensure that pumps are promptly returned to service when issues arise.
Comments