what is a hydraulic component test stand
- ADMIN
- Jul 4, 2023
- 5 min read
A hydraulic component test stand is a specialized equipment used in the aerospace, automotive, and industrial sectors to test and evaluate the performance and reliability of hydraulic components. It is designed to simulate real-world operating conditions and assess the functionality, durability, and efficiency of hydraulic components such as pumps, valves, cylinders, motors, and actuators.
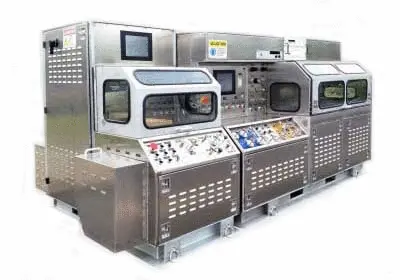
Hydraulic component test stands are equipped with a range of instruments and control systems that allow for precise monitoring and measurement of various parameters, including pressure, flow rate, temperature, and vibration. They are capable of subjecting the hydraulic components to a wide range of operating conditions, including different pressures, temperatures, and flow rates, to evaluate their performance under varying loads and stress levels.
The test stand typically consists of a hydraulic power unit that generates the required hydraulic pressure and flow, along with a control panel that allows operators to set and adjust test parameters. It also includes a series of valves, actuators, and sensors to simulate the actual working environment and provide accurate feedback on the component's performance.
The main purpose of a hydraulic component test stand is to ensure that hydraulic components meet the required performance specifications and industry standards before they are deployed in operational systems. By subjecting the components to rigorous testing, manufacturers can identify any design flaws, manufacturing defects, or performance issues and make necessary improvements or adjustments.

In addition to evaluating the performance of hydraulic components, test stands are also used for research and development purposes. They enable engineers to study the behavior of hydraulic systems, optimize component designs, and develop new technologies to enhance the efficiency and reliability of hydraulic systems. Hydraulic component test stands are essential tools in the field of hydraulics, allowing manufacturers and engineers to validate the performance and quality of hydraulic components before they are integrated into larger systems. They play a crucial role in ensuring the safety, reliability, and efficiency of hydraulic systems used in various industries.
Several aircraft checks and maintenance procedures require the use of hydraulic component test stands. Here are some examples: Landing Gear Checks: Hydraulic component test stands are used to test the landing gear hydraulic actuators and valves. These tests ensure proper extension and retraction of the landing gear and verify the functionality of the hydraulic systems responsible for landing gear operation.
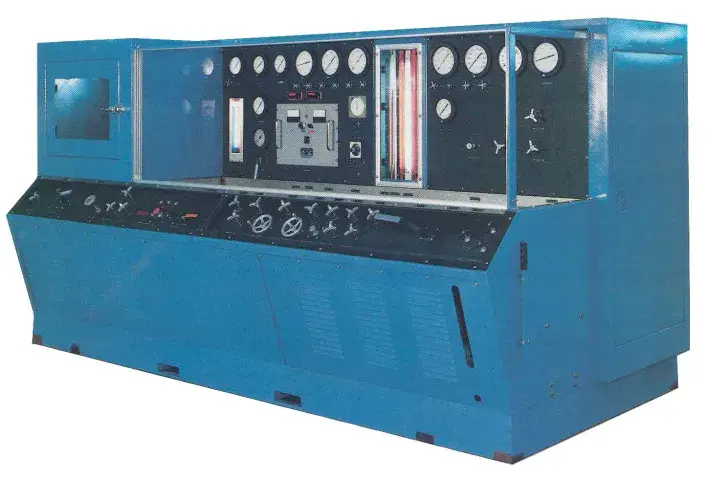
Flight Control System Checks: Hydraulic components such as hydraulic pumps, control valves, and actuators in the aircraft's flight control system are tested using hydraulic component test stands. This ensures that the flight control surfaces, such as ailerons, elevators, and rudders, operate smoothly and accurately. Braking System Checks: The hydraulic components in the aircraft's braking system, including brake cylinders and valves, are tested using test stands. This helps evaluate the braking system's efficiency, response time, and overall performance. Thrust Reverser Checks: Hydraulic actuators and valves in thrust reverser systems are tested using test stands to ensure proper deployment and retraction of the thrust reversers, which are essential for aircraft deceleration after landing. Cargo Door Checks: Hydraulic systems involved in the operation of cargo doors, such as actuators and control valves, are tested to ensure smooth and reliable opening and closing of the doors. Hydraulic System Maintenance: During routine maintenance of the aircraft's hydraulic system, components such as hydraulic pumps, motors, valves, and actuators are tested using test stands to assess their performance and detect any abnormalities or malfunctions. Hydraulic component test stands are versatile tools that can be used for various aircraft checks and maintenance procedures, ensuring the proper functioning of hydraulic systems and components critical to the aircraft's operation and safety.
Aircraft checks that require the use of component test stands are typically associated with specific maintenance checks known as "C-checks" and "D-checks." These checks are comprehensive inspections performed at regular intervals to ensure the airworthiness and reliability of the aircraft.
During C-checks and D-checks, various components of the aircraft, including hydraulic systems, are thoroughly examined and tested. Hydraulic component test stands play a crucial role in assessing the performance and functionality of hydraulic components such as pumps, actuators, valves, and cylinders.
It's important to note that the specific terminology and naming conventions for aircraft checks may vary among different aircraft operators and regulatory authorities. However, C-checks and D-checks are commonly used terms to refer to major maintenance inspections that involve the use of component test stands to evaluate hydraulic systems and components.
Component test work is typically performed by qualified aviation technicians or engineers who specialize in maintenance, repair, and overhaul (MRO) activities. These professionals have in-depth knowledge and expertise in the specific aircraft systems and components being tested.
Within an MRO facility or an aircraft maintenance organization, there may be dedicated teams or departments responsible for conducting component tests. These teams may include technicians, engineers, and quality control personnel who are trained in the proper procedures for testing and evaluating various aircraft components.
Additionally, component testing may also be outsourced to specialized MRO service providers who have the necessary equipment, expertise, and certifications to perform these tests. These external providers may offer specialized testing services for specific components or systems and may have the capabilities to conduct tests on behalf of multiple aircraft operators.
In either case, the individuals or organizations conducting component test work must adhere to industry standards and regulatory requirements to ensure the accuracy and reliability of the test results. This helps to maintain the safety and airworthiness of the aircraft components being tested.
Component testing involves evaluating various parts of an aircraft component to ensure their functionality, reliability, and adherence to specifications. The specific parts tested may vary depending on the type of component and the requirements of the test. Here are some common component test parts: Mechanical Parts: This includes testing the mechanical integrity and performance of components such as gears, bearings, shafts, valves, actuators, hinges, and structural elements. Electrical Components: Electrical testing involves evaluating the functionality, insulation resistance, continuity, and electrical characteristics of components like connectors, cables, switches, relays, circuit breakers, and control panels. Fluid Systems: Component testing may involve assessing the performance and integrity of fluid systems, including hydraulic and pneumatic components such as pumps, valves, hoses, filters, pressure regulators, and accumulators. Sensors and Instruments: Testing of sensors and instruments focuses on their accuracy, sensitivity, response time, and calibration. This can include components like pressure sensors, temperature sensors, flow meters, accelerometers, and gyroscopes. Electronic Circuitry: For electronic components, testing may involve assessing the functionality, performance, and reliability of circuit boards, integrated circuits, microprocessors, memory modules, and other electronic parts. Software and Firmware: Component testing may also involve evaluating the software or firmware embedded in electronic components, ensuring proper operation, compatibility, and adherence to specified standards. Environmental Conditions: Some component tests assess performance under various environmental conditions, such as temperature extremes, humidity, vibration, shock, and electromagnetic interference (EMI). These are just some examples of the component test parts that may be evaluated during the testing process. The specific parts tested will depend on the nature of the component, its criticality, and the requirements outlined in the maintenance procedures or regulatory guidelines.
Kommentare